The 'Bridge' to Kashmir is almost ready
Aug 10, 2022
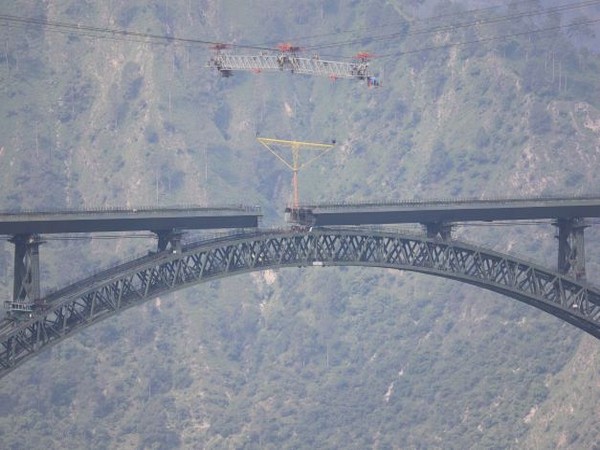
New Delhi [India] August 10 : For the first time ever since independence, Srinagar will be linked to the rest of India after the overarch deck on the world's highest single-arch railway bridge over Chenab River will be launched on August 13.
The 1.315 km long bridge which is being built at a dizzying height of 359 meters is even taller than Eiffel Tower. It will connect the Salal-A and Dugga railway stations on either side of the bridge with the mighty River Chenab in Reasi district. The moment will be marked with a golden joint and is seen as the symbol of national integration.
The bridge is the tallest railway bridge in the world and is being constructed by the Northern Railway at an estimated cost of Rs 28,000 crore as part of the Udhampur Srinagar Baramulla Rail Link Project.
Named 'Chenab Bridge', this railway bridge will be 359 meters higher than the water level of the Chenab river and its length will be 1315 meters. The highest railway bridge at the time is located on the Bepanjiang River in Guizhou Province, China, with a height of 275 meters above the water level. It is a major achievement towards the completion of the 111 km long Katra-Banhal railway section, for which massive Himalayan Hills are being mined.
The installation of the arch before the construction of the deck was one of the biggest civil engineering challenges in the recent history of India, with a 5.6-meter span at the top of the bridge being connected at the center on both sides. Out of the 111 km. There is 97 km of tunneling which is more than 85%. Tunneling on this scale has not been done in any other part of the country. About 86 km of tunneling work has been completed so far. Built on Darya Chenab, the arch of this bridge is capable of withstanding winds of 266 kilometers per hour.
The length of the bridge is 1315 meters. The number of pillars is 17. 28,660 metric tons of steel were used in its construction, at an estimated cost of Rs 1,486 crore. The weight of the installed arch is 10,619 metric tons. The steel used in the structure is suitable for temperatures ranging from minus 10 degrees Celsius to minus 40 degrees Celsius. The bridge will have a minimum lifespan of 120 years and will be built for trains at a speed of 100 km.
This bridge has the ability to withstand winds of 266 kilometersper hour and withstand blast load and withstand severe earthquakes.
The bridge has 93 deck segments, each weighing about 85T, launched simultaneously on reinforced steel arches from both ends, and work is underway on five. The two ends will eventually be joined with 'High Strength Fraction Grip' (HSFG) bolts to complete the upper deck of the bridge.
The bridge has been constructed by Afcons, a Mumbai-based company.
Gary Dhar Raja Gopalan, Deputy Managing Director of African Company said, " When we finished the arch closure last year, it gave us huge relief in terms of our competency to finish the project with such accuracy that there was no mismatch. And that gave us a lot of confidence to tackle the balance part of the project very comfortably. Together with NR and KRCL, we are eagerly looking forward to the forthcoming milestone of the golden joint."
"The bridge superstructure on the arch was being incrementally pushed from two ends of the Chenab River valley, and it will finally meet at the middle of the arch. "To push it to ensure that it has all the coordinates perfect, and meets and joins is itself a golden joint. Once the golden joint is completed we can safely say that the bridge is about 98% complete," he added.
Earlier, appreciating the role of Northern Railway and Konkon Railway Corporation in finalizing the design of the Chenab Bridge, he further said, "We were assisted in technical issues, approval of drawings, etc. by Northern Railway and Konkon Railway Corporation (KRCL) which created local employment." KRCL constructed roads to reach the project site till the construction of this bridge. This provided connectivity to remote areas of the region.
According to him, the Northern Railway allowed them to use a Phased Array Ultrasonic Testing Machine for inspection of welds, a first in India. A fully equipped NABL laboratory was set up for the first time in India to ensure that quality was monitored at every stage of the project, even over time.