Tirupur: A shining global example of sustainability
Nov 19, 2022
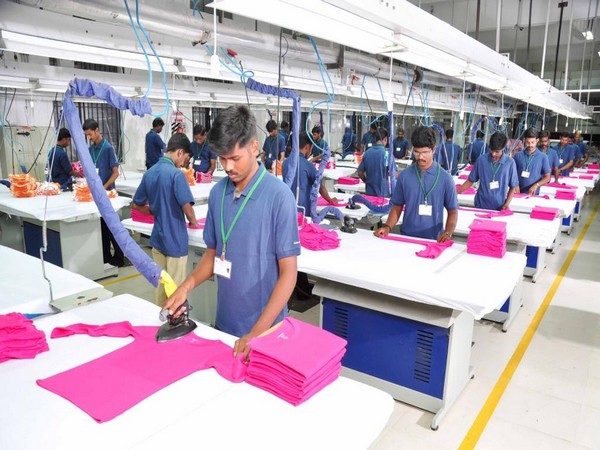
Tirupur (Tamil Nadu) [India], November 19 : Tirupur has set a precedent by emerging as a truly sustainable global apparel-making hub.
The knitwear cluster Tirupur in southern India has today emerged as a completely transformed global apparel manufacturing hub in the country.
From hosting one of the most polluting textile value chain till a few years back (which had evoked massive protests by local farmers and other communities; followed by Madras High Court order directing closure of 750-odd dyeing and bleaching units in this cluster for not complying with the State Pollution Control Board's zero-liquid discharge (ZLD norms), Tirupur is currently a completely 'Zero Liquid Discharge' garment cluster where water used by its dyeing and processing units are treated at common affluent treatment plants and reused.
By doing so, the cluster is not only consuming significantly less water, but is also not discharging any hazardous water.
Having emerged as a sustainable sourcing destination for knitwear, the Rs 60,000-crore business which exports half of its production to the global market, Tirupur Cluster is currently having 300 dyeing units attached with 18 Common Effluent Treatment Plants (CETPs) and 60 dyeing units having their own Individual Effluent Treatment Plants (IETPs).
The CETPs and IETPs in Tirupur have successfully implemented Zero Liquid Discharge (ZLD), first of its kind globally. Every day 18 CETPs are recycling 100 MLD of water and 60 IETPs are recycling 20 MLD of water. The effluent is treated to recover 94 per cent of water, which is re-sent for processing and the balance 6 per cent recovered as salt solution or salt to reuse for process.
"We as a cluster have shown a great degree of resilience and perseverance to reach where we are today. We are proud to transform Tirupur as a green hub where most of the resources are used in a sustainable manner. Initial years were really difficult as these dyeing units were in no position to comply with ZLD requirements. But we have managed to overcome all our challenges to set up one of the most sustainable circular fashion supply chains," says K M Subramanian, President, Tirupur Exporters Association (TEA) and managing director of Rs 750 crore KM Knitwear, which exports 50 per cent of its knitwear production to the global market.
"For the last 10 years, we have been strictly pursuing our ZLD model and along the way we have also taken up multiple projects which are aimed at reducing our carbon footprint significantly. As a green cluster, we have gone much ahead," says A Sakthivel, President, Federation of Indian Export Organizations; chairman, Apparel Export Promotion Council and founding president of TEA.
Kumar Duraiswamy, joint secretary, TEA says that the toxic effluents generated during the processing of fabrics was depleting the ground water level before implementation of ZLD, which has now been completely eliminated and the treated water is reused again for processing of Fabrics.
"Our efforts have paid off. Apart from successful implementation of ZLD, we are doing multiple things to positively impact our surroundings and environment. In fact, we have set a precedent that others can also emulate and help build a more sustainable ecosystem for the industry," states N. Thirukkumaran. General Secretary, TEA.
"Tirupur as a knitwear hub has come a long way. Each and every stakeholder has played its role in making this cluster a truly sustainable garment manufacturing cluster. We will continue to carry on with our endeavour to take this success story to the next level," says Gopalakrishnan, Chairman of Tirupur-based, Royal Classic Mills. Led by flagship knitwear brand like Classic Polo, the Rs 750-crore company boasts of having the largest IETP in Tirupur.
Besides, ZLD implementation, Tirupur units have installed both solar power plants and wind energy generators, producing 1,600 KVA per day, whereas the power consumption of the industry in the Tirupur cluster is about 250 KVA only.
Moreover, the overall power consumption of entire Tirupur district is 650 KVA and hence the excess green power produced is distributed through Tamil Nadu Power Grid.
In another significant initiative called `Vanathukul Tirupur', a mass tree plantation drive has been carried out by an NGO called VETRY. Supported by Tirupur garment units, VETRY, in last 8 years, has planted 15 lakh saplings.
Rainwater harvesting is one of the major activities being followed widely in the cluster. In the last few years, the amount of rainwater harvested has many factories self-sufficient in terms of water usage.